Lean is a methodology that emphasizes maximizing value by minimizing waste. It originated in manufacturing but has since been adopted across various industries. The core principle of Lean is to streamline processes, eliminate inefficiencies, and enhance customer satisfaction. By focusing on what truly adds value, organizations can improve their operations and deliver better products and services. This approach not only fosters a culture of continuous improvement but also empowers teams to identify and solve problems proactively.
Lean vs Six Sigma
While both Lean and Six Sigma aim to improve processes, they do so through different lenses. Lean focuses on reducing waste and enhancing flow, whereas Six Sigma emphasizes reducing variation and improving quality. When combined, these methodologies can create a powerful toolkit for operational excellence. Understanding the distinctions and synergies between Lean and Six Sigma can help professionals tailor their strategies for optimal results.
Lean vs Agile
Lean and Agile share a common goal of improving efficiency and responsiveness, but they cater to different contexts. Lean is primarily concerned with process optimization and waste reduction, while Agile focuses on flexibility and iterative development, particularly in software and project management. Both methodologies can coexist and complement each other, allowing organizations to adapt quickly to changing market demands while maintaining a streamlined operation.
Leveraging tools that embody Lean principles is crucial for success. No-code and low-code platforms, such as Airtable and Zapier, enable teams to implement Lean practices without extensive coding knowledge. These tools enhance agility, reduce costs, and improve user experiences, making them invaluable for professionals striving to optimize their operations.
Applications
- Streamlining workflows: By applying Lean principles, teams can identify bottlenecks in their workflows, allowing them to streamline processes and enhance overall efficiency. This means less time spent on unnecessary tasks and more time delivering value to stakeholders.
- Enhancing cross-functional collaboration: Lean encourages teams to work together to eliminate waste. By fostering a culture of collaboration, businesses can break down silos, ensuring that everyone is aligned and focused on common goals, ultimately leading to faster decision-making and improved outcomes.
- Implementing continuous improvement: Lean's emphasis on continuous improvement empowers teams to regularly assess their processes and identify areas for enhancement. This proactive approach not only boosts productivity but also cultivates a mindset of innovation and adaptability within the organization.
- Optimizing resource allocation: Lean helps teams analyze resource utilization, ensuring that time, budget, and personnel are allocated effectively. By minimizing waste, teams can redirect resources toward high-impact initiatives that drive business growth.
- Leveraging data for informed decisions: Lean methodologies encourage the use of data to identify inefficiencies and track progress. Businesses can harness this data to make informed decisions, ensuring that their strategies are grounded in reality and aligned with organizational objectives.
For Business Operators
Expert Bizops help: Learn, Connect, Integrate
Glossary
Common terms and jargon for the Business Operator.
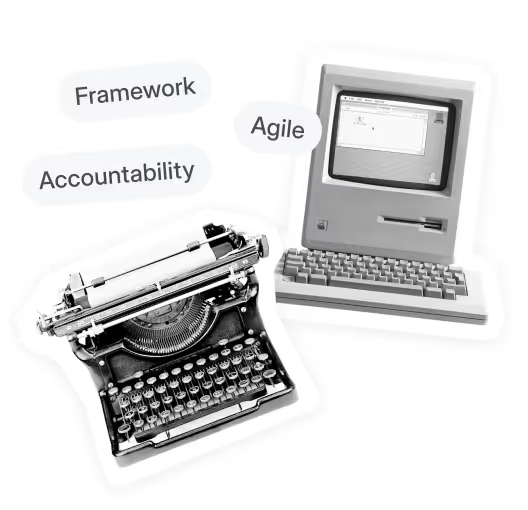
We created this resource for people like you: learning, designing, building Bizops.