Six Sigma is a data-driven methodology designed to improve processes by minimizing defects and enhancing quality. It employs statistical tools and techniques to identify and eliminate the root causes of errors, leading to more efficient operations and better outcomes. By focusing on process improvement, organizations can achieve significant cost savings and boost customer satisfaction, making it a vital approach for any operations professional looking to drive excellence.
Six Sigma tools
A variety of tools are integral to the Six Sigma approach, enabling teams to analyze data and streamline processes effectively. Commonly used tools include DMAIC (Define, Measure, Analyze, Improve, Control), which provides a structured framework for problem-solving. Other essential tools are process mapping, root cause analysis, and control charts, which help visualize performance and identify areas for improvement. Modern no-code platforms and low-code platforms, such as Airtable and Monday.com, can facilitate the implementation of these tools, allowing teams to adapt quickly without extensive coding knowledge.
Key concepts of Six Sigma
At its core, Six Sigma revolves around the concept of reducing variation and improving process capability. The methodology is often represented by the sigma symbol (σ), which denotes standard deviation in statistics. A Six Sigma process aims for a defect rate of fewer than 3.4 defects per million opportunities, signifying a high level of quality. This focus on precision and consistency is crucial for organizations striving to meet customer expectations and maintain a competitive edge.
Importance in operations
For operations professionals, understanding and applying Six Sigma principles can be a game-changer. The ability to leverage data and statistical analysis not only enhances process efficiency but also fosters a culture of continuous improvement. As teams adopt these methodologies, they can better align their objectives with organizational goals, ultimately leading to improved performance and user experiences. In a landscape where agility and cost-effectiveness are paramount, Six Sigma stands out as a powerful tool for driving operational success.
Applications
- Streamlining processes: By applying Six Sigma methodologies, teams can identify inefficiencies in workflows, leading to smoother operations and reduced cycle times. This means less time spent on tasks and more time for strategic initiatives—who doesn't want that?
- Enhancing data analysis: Six Sigma's focus on data-driven decision-making empowers professionals to leverage statistical tools for deeper insights. This can help in making informed choices that align with business goals, ultimately driving better outcomes.
- Improving customer satisfaction: With a goal of fewer than 3.4 defects per million opportunities, Six Sigma helps teams enhance product and service quality. Happy customers are repeat customers, and that’s a win for everyone involved.
- Fostering a culture of continuous improvement: Implementing Six Sigma encourages teams to regularly assess and refine their processes. This mindset not only boosts morale but also keeps the organization agile and competitive in a fast-paced market.
- Aligning objectives with organizational goals: Six Sigma provides a structured approach to problem-solving, ensuring that initiatives are directly tied to broader business objectives. This alignment is crucial for maximizing impact and achieving strategic success.
For Business Operators
Expert Bizops help: Learn, Connect, Integrate
Glossary
Common terms and jargon for the Business Operator.
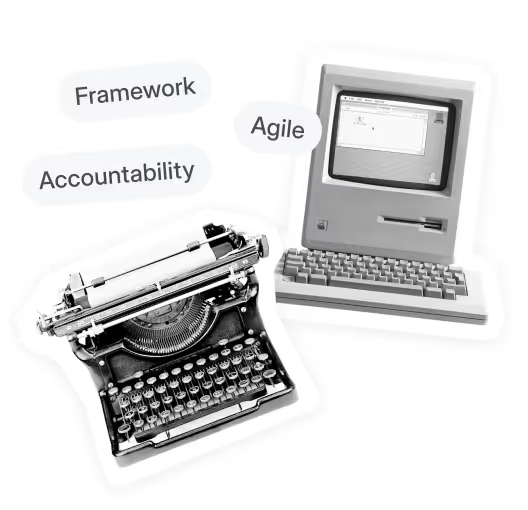
We created this resource for people like you: learning, designing, building Bizops.