Lean methodology is a systematic approach aimed at minimizing waste while maximizing value in processes and operations. It emphasizes efficiency, continuous improvement, and delivering quality products or services to customers. By focusing on eliminating non-value-added activities, organizations can streamline their operations, reduce costs, and enhance overall performance. This methodology is not just about cutting corners; it's about creating a culture of innovation and responsiveness that can adapt to changing market demands. Lean methodology originated in manufacturing but has since been adopted across various industries. It involves principles such as value stream mapping, which helps identify areas of waste, and the concept of "just-in-time" production, ensuring that resources are used only when needed. The goal is to create a smooth flow of work that enhances productivity and customer satisfaction. By fostering a mindset of continuous improvement, teams can identify inefficiencies and implement solutions that lead to better outcomes.
Key concepts of Lean Methodology
Central to Lean methodology are several key concepts, including the 5S system (Sort, Set in order, Shine, Standardize, Sustain), which promotes organization and efficiency in the workplace. Another important aspect is the focus on customer value, ensuring that every step in a process adds value from the customer's perspective. This customer-centric approach not only improves service delivery but also strengthens the relationship between the organization and its clients.
Applications of Lean Methodology
While Lean methodology has its roots in manufacturing, its principles can be applied to various sectors, including healthcare, software development, and service industries. The adaptability of Lean practices allows organizations to tailor their approach to specific challenges, enhancing agility and responsiveness. Leveraging Lean methodology can lead to significant cost savings and improved user experiences, making it an essential tool for professionals looking to optimize their operations.
In summary, Lean methodology is a powerful framework for enhancing efficiency and value in any organization. By embracing its principles, teams can foster a culture of continuous improvement that not only drives operational excellence but also positions them for long-term success in a competitive landscape. As professionals navigate the complexities of modern business, tools, and methodologies like Lean become indispensable for achieving their goals and delivering exceptional results.
Applications
- Simplifying processes: By applying Lean methodology, teams can identify and eliminate bottlenecks in workflows, ensuring that tasks flow smoothly and efficiently. This not only saves time but also enhances team morale when they see their efforts translating into tangible results.
- Enhancing customer feedback loops: Lean emphasizes customer value, which means teams can implement regular feedback mechanisms to ensure that products and services meet client expectations. This iterative approach allows for quick adjustments, keeping customers happy and engaged.
- Implementing 5S for organization: The 5S system (Sort, Set in order, Shine, Standardize, Sustain) can be a game-changer for teams. A tidy workspace leads to clearer thinking and faster execution, making it easier to focus on high-impact tasks rather than searching for misplaced documents or tools.
- Data-driven decision making: Lean methodology encourages continuous improvement through data analysis. Teams can leverage metrics to identify inefficiencies and make informed decisions, ensuring that every action taken is backed by solid evidence rather than gut feelings.
- Fostering a culture of innovation: By embracing Lean principles, teams can create an environment where team members feel empowered to suggest improvements and experiment with new ideas. This culture of innovation not only drives operational excellence but also positions the team as a proactive force within the organization.
For Business Operators
Expert Bizops help: Learn, Connect, Integrate
Glossary
Common terms and jargon for the Business Operator.
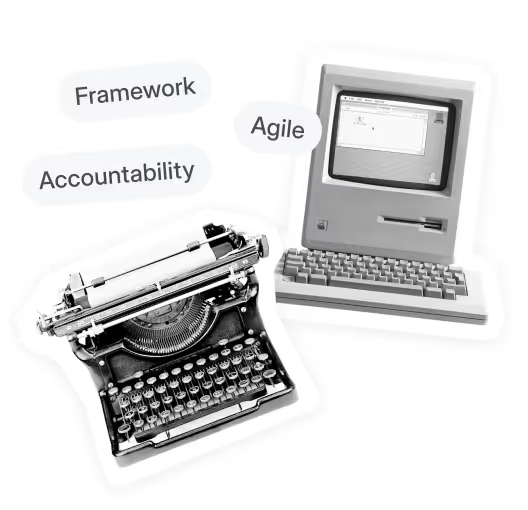
We created this resource for people like you: learning, designing, building Bizops.